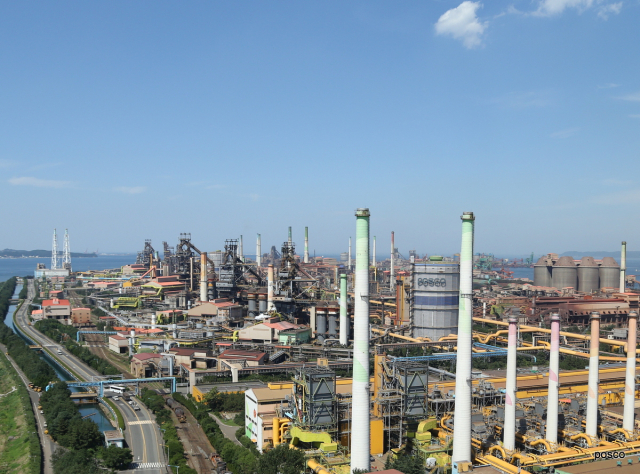
포항제철소의 제2고로는 ‘스마트 용광로’로 불린다. 수십년간 쌓인 빅데이터를 기반으로 인공지능(AI) 기술을 접목해 원료의 양, 쇳물의 온도, 통기성 등 각종 지표를 모두 정형화·표준화하는 데 성공했다. 균일한 품질의 철강을 생산하려면 쇳물 온도를 일정하게 유지하는 것이 중요하다. 고로의 쇳물에 문제가 생길 경우 제철소는 ‘올 스톱’된다.
과거에는 전담 작업자가 1시간마다 쇳물 온도를 체크하며 품질을 챙겼지만 지금은 수많은 AI 센서들이 실시간으로 상황판에 용광로 상태와 정보를 그려낸다. 포스코는 세계 최고의 기술력을 바탕으로 ‘제2의 창업’에 버금갈 도약에 나서고 있다.
◇고품질 표준화로 조강 생산량 12억 톤 눈앞=설비의 스마트화는 고품질 철강 생산의 효율성을 획기적으로 끌어올렸다. 포스코의 지난해 기준 누적 조강 생산량(포항·광양 제철소 합산)은 약 11억 8000만 톤에 달한다. 2019년 누계 10억 톤을 달성한 데 이어 설비 고도화를 통해 5년 만에 2억 톤 가까이를 추가 생산했다.
포스코의 ‘품질 제일주의’는 작은 허점도 용납하지 않았던 박태준 창업자의 완벽주의에서 출발한다. 포스코 명예회장인 창업자는 건설 일정에 쫓기면서도 포항 3기 공사 현장에서 작은 부실시공 흔적을 발견하자 직접 다이너마이트를 가져와 공정이 80% 진행된 설비를 폭파 후 다시 짓게 했다. 품질을 지키려는 뚝심은 포스코가 고급강 제품 부문에서 글로벌 경쟁력을 갖추는 근간이 됐다. 포스코는 현재 고부가 자동차 강판 생산 규모 기준 전 세계 2위 철강사다.
◇적극적 해외 진출로 글로벌 외연 확장=공격적 해외 투자와 인수합병(M&A)은 포스코의 철강 본원 경쟁력 강화로 이어졌다. 특히 2010년 대우인터내셔널(포스코인터내셔널(047050)) 인수는 글로벌 판매 채널 확대와 그룹사 시너지 창출의 기폭제가 됐다. 포스코인터내셔널 인수를 기점으로 40조 원대에 머물던 포스코의 매출(연결 기준)은 60조 원대로 ‘퀀텀점프’했다.
포스코홀딩스의 지난해 매출액은 72조 6880억 원, 영업이익은 2조 1750억 원을 각각 기록했다. 늘어난 영업이익은 다시 해외 설비투자 확대에 투입된다. 포스코는 인도네시아에 동남아시아 최초의 일관제철소를 건설했고 튀르키예·베트남 등지에 냉연 공장, 멕시코에 해외 최초의 자동차 강판 공장을 완공했다. 지금도 인도에 새 일관제철소 건설을 추진 중이며 미국에 전기로 기반 제철소 진출도 검토하고 있다.
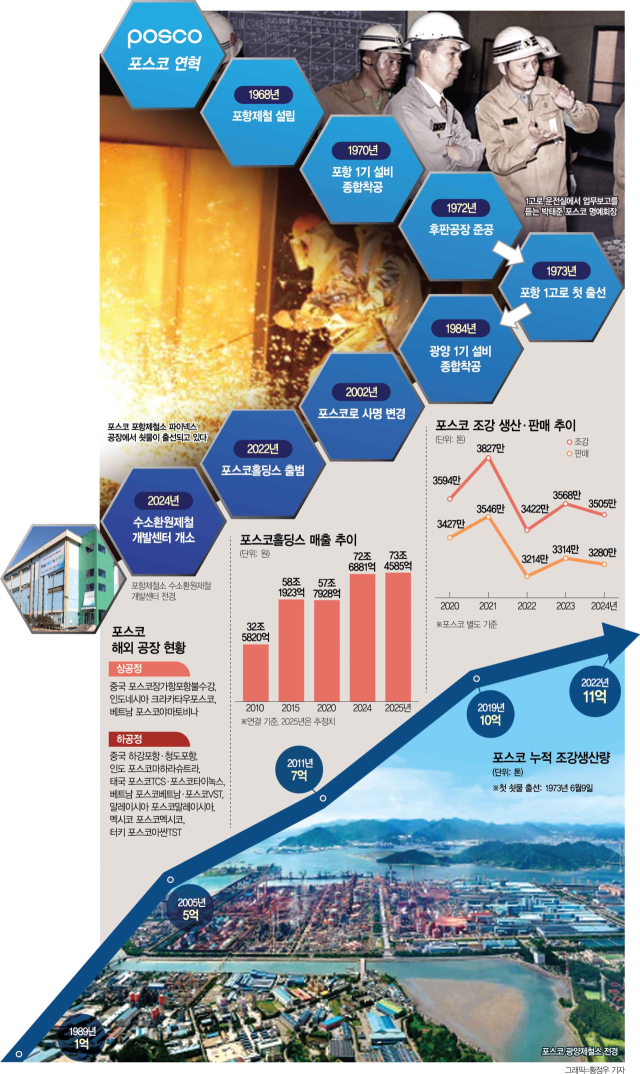
◇미래형 제철소 이끄는 수소와 AI=수소환원철과 AI 기술은 포스코가 준비하는 미래 제철소의 양대 축이다. 포스코는 이산화탄소 배출량이 많은 석탄 이용을 줄이고 수소를 연료로 철강 제품을 만드는 체제 전환을 필두로 AI와 로봇으로 작업장 효율성과 안전성을 높이는 업무 개선에 주력하고 있다.
하이렉스(HyREX)는 포스코가 독자 기술을 바탕으로 개발 중인 한국형 수소환원제철 기술이다. 철광석과 석탄을 이용한 기존의 철강 생산 방식은 필연적으로 이산화탄소를 발생시키지만 하이렉스는 수소를 사용하기 때문에 배출물이 물뿐이다. 철광석을 고온 가열된 수소와 접촉시켜 제조한 철을 직접환원철(DRI)이라고 하는데 이 DRI를 만들어낼 환원로를 만드는 것이 기술의 정수다.
전 세계적으로 100% 수소만을 사용해 DRI를 만드는 환원로는 아직 상용화되지 않았다. 전 세계 유수 철강사들이 개발 경쟁을 벌이는 가운데 하이렉스는 유럽과 미국 등에서 개발 중인 ‘샤프트 환원로’ 기술에 비해 원료 사용, 제품 품질, 제조 원가 측면에서 경쟁 우위에 있는 것으로 평가받고 있다.
◇‘인텔리전트 팩토리’로 혁신과 안전 다 잡아=인텔리전트 공장은 단순히 프로세스가 자동화된 스마트팩토리를 넘어 전 공정에서 발생한 데이터를 자동으로 수집해 분석하고 의사 결정까지 내리는 지능형 제철소다. AI가 생산 현장에서 카메라와 센서 등을 통해 쇳물의 최적 온도와 원료 수급 타이밍, 생산량 등을 파악한다.
제철소 곳곳에서 업무를 수행 중인 4족 보행 로봇도 볼 수 있다. 미국 보스턴다이내믹스에서 도입한 로봇 개 ‘스팟’은 쇳물이 만들어지는 용광로 주변 등 위험한 현장에서 사람 대신 활동하고 있다. 1200도에 달하는 열풍이 지나는 44개의 연결통로를 따라 배치된 스팟은 온도와 가스 및 냉각수 누출 유무 등을 점검하고 있다.
외부 로봇 업체와 3년간 공동 개발한 스마트와이어볼은 석탄·철광석 등 원료를 옮기는 컨베이어벨트의 상태를 점검한다. 이전에는 포항과 광양 제철소에서 각각 수십 명의 작업자가 300㎞에 달하는 컨베이어벨트를 수작업으로 진단했다. 이제는 스마트와이어볼이 음향·영상·열화상 센서를 통해 설비를 안전하게 관리한다. 지난해 스마트와이어볼을 설치해 실증 테스트를 마친 포스코는 올해 도입을 확대할 계획이다.